What is Aluminum Coil?
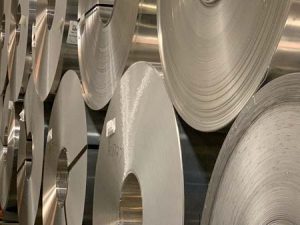
Raw aluminum coil which may be supplied to a manufacturer as shown, or processed further at the mill
Aluminum coil can be produced from aluminum ingots or other forms of raw aluminum (called cold rolling or direct cast) or from a smelting process directly through rolling (called continuous cast). These sheets of rolled aluminum are then rolled up, or coiled, around a core. These coils are densely packed, making them easier to ship and store when compared to aluminum in sheet form. Coil is used to manufacture an almost unlimited range of components used in an extensive number of industries.
Pure aluminum is too soft for most manufacturing applications. Therefore, most aluminum coil is manufactured and supplied as an alloy. These alloys composed of at least two or more elements of which at least one is aluminum. Aluminum alloys for sheet products are identified by a four digit numerical system which is administered by the Aluminum Association. When alloyed with other metals, aluminum’s mechanical and other properties can be tailored to meet specific requirements for strength, formability, and other properties.
Aluminum coil is available in variable lengths, widths and thicknesses, also referred to as “gauge”. The exact dimensions are determined by the size of the components being made, and the manufacturing process that is used to produce them. Several surface finishes are available including mill, matte and bright. Selection will depend on the use and desired look of the finished part.
Aluminum coil is also offered in various tempers. It may be provided “as fabricated”, called “F” temper, which has no defined mechanical limits, and where no special control has been applied over thermal or work-hardening conditions. Since this approach is subject to variability, it’s usually used for products that are at intermediate stages of production. Strain-hardened is another option, which applies to wrought products which are strengthened by cold-rolling or cold-working. The aluminum may also be annealed, meaning the material has been heated with controlled conditions to produce the desired combination of strength and formability.
Why Choose Aluminum over Other Metals?
-
Weight – The biggest advantage that aluminum has over most competing materials with similar properties is its lighter weight. This makes it ideal for applications such as auto, aerospace and others where total product weight is of concern. It’s also more economical to ship as a result.
- Workability – aluminum is very malleable, meaning it could easily be formed, stamped or shaped as needed. Its workability and versatility contribute greatly to its popularity. Aluminum is preferred for many manufacturing processes, such as drawing, roll forming, and stamping.
- Corrosion Resistance – it also is resistant to corrosion and rust, giving it a significant edge over steel.
- Value – aluminum costs considerably less than materials such as copper, allowing manufacturers to keep material expenses down without sacrificing performance.
- Recyclability – aluminum is easily recycled allowing it to be used again and again thus reducing environmental impact.
- Conductive Properties – Aluminum is a good conductor of heat and electricity. When measured by equal cross-sectional area, electrical grade aluminum has conductivity equal to 62% of electrical grade copper. However when compared using equal weights of both, the conductivity is 204% of copper.
What is Aluminum Coil Used For?
Coil is used for many industries and applications. It is the preferred material for many stamped and formed components in electronics, medical, transportation and other fields.
Stacked aluminum coil, ready to ship
Transportation – As mentioned earlier, it is widely used for transportation. In the auto industry, it is used to make anything from wheel hubs and radiators to engine components and car doors, and anything in between. As the automotive industry strives to reduce vehicle weight, the use of aluminum to replace heavier metals can offer significant weight reductions. This effort to optimize all components to be the lightest possible weight is also referred to as “lightweighting”.
- Electronics – since aluminum is a good conductor of electricity, holds heat and resists corrosion, it is found in many industrial and consumer electronics. It can be used to make anything from heat sinks, stamped components and shielding to larger components such as enclosures.
- Consumer Goods and Hardware – Aluminum components produced from coil can be found in health and beauty item packaging, tools and other hardware, building applications, jewelry, and an enormous array of other common items.
- Medical – aluminum is widely used in the medical and dental fields for many products ranging from disposables to surgical equipment and sophisticated electronic devices.
- Aerospace – Because of aluminum’s light weight, corrosion resistance, and potential strength characteristics, some alloys and tempers are ideal for aerospace applications.